DXユースケース
製造業 ものづくりDX × カーボンニュートラル
現場改善×CO₂排出量の削減
自社の排出量(Scope1・2)を削減していくためには、製造現場のカイゼンが不可欠です。製造現場のカイゼンにつながる製造DXの取り組みと脱炭素化につながる取り組みを両輪で進めることでお客さまの企業価値・競争力向上を実現します。
1.不良品発生の原因特定・改善によるCO₂排出量の削減
不良原因の調査は、工程間の情報収集を人手で行っていたり、バラバラになった紙やシステムなどの情報を集めて調査・分析を行っている場合があり、時間を要してしまいます。
複数工程における情報を収集し、散布図、ヒストグラム、トレンドグラフによって品質検査実績と加工実績の相関確認や品質結果に影響を与えている加工条件の見直しを実施することで、不良品の発生原因を特定し改善を行います。それにより不良品数を削減し、CO₂排出量削減につなげることができます。
製造現場の課題
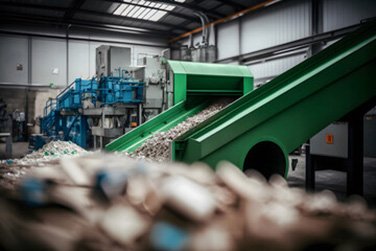
-
不良原因調査を人手で実施しているため、現場作業員の負荷が大きい
-
情報が点在化しており、情報を集めて分析するのに時間がかかる
-
原因調査に時間がかかるため、不良が発生しても対処療法にとどまっている
-
不良発生時の原因特定を熟練技術者の経験と勘で行っている
データ活用による対策
生産現場で発生した実績データを集めた「統合データモデル」で一元管理することにより、複数工程にまたがる不良品の発生原因を容易に特定することができます。
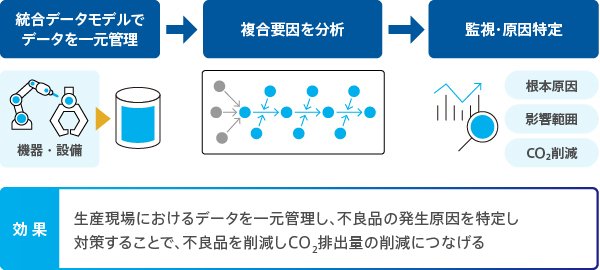
2.設備・工程ごとの稼働ロスを軽減して CO₂排出量を削減
製造現場の改善には、まず現場のデータを収集して見える化していくことが必要になりますが、設備や機器のメーカー・種類が違うためデータ取得方法・形式が異なり、 設備や工程ごとの稼働状況・ エネルギー消費量の把握が難しい場合があります。そこで、さまざまな設備から容易にデータを 収集可能な PLC ゲートウェイ※を活用し、設備のエネルギー消費量や稼働状況などを見える化し、製造現場の改善につなげることでCO₂排出量を削減します。
※PLCゲートウェイ:多種多様な規格のセンサーやコントローラを、ネットワークに接続する機器のこと
製造現場における課題
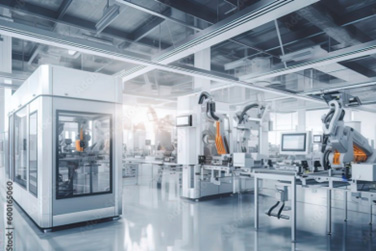
-
設備単位で、稼働状況やエネルギー使用量を把握したいが、どのようにデータを取ればよいか分からない
-
目視で確認した状況を手作業で記録しているため、作業員の負担が大きく、ミスも生じやすい
-
稼働ロスやエネルギーロスの理由がわからず、改善につなげるための分析ができない
-
リアルタイムに情報が把握できないため、改善につなげにくい
データ活用による対策
さまざまな設備から容易にデータを収集可能な PLC ゲートウェイを活用し、設備のエネルギー消費量や稼働状況などを見える化します。
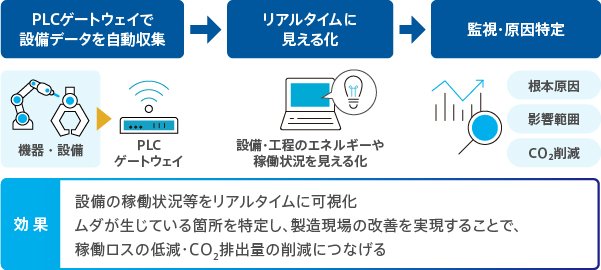
データにもとづく工場マネジメント
業務データ、計画データおよびリアルタイムに収集した5M1Eにもとづく現場ものづくり情報などの多様なデータを活用可能な状態に蓄積、集約することで、迅速に精度の高い工場のマネジメントが可能になります。
1.工場の設備総合効率を把握し、生産効率を改善
製造現場では、設備故障により生産工程に遅延が発生したり、故障に対してカン・コツで対応するため、抜本的な対策が打てないなどの事象が発生しています。
また、工場のボトルネックがどこにあるのかわからず、どこから対策を打つべきか、といった問題があり、停止ロスや性能ロスを削減し、設備の時間稼働率/性能稼働率を改善する取り組みが必要です。
製造現場における課題
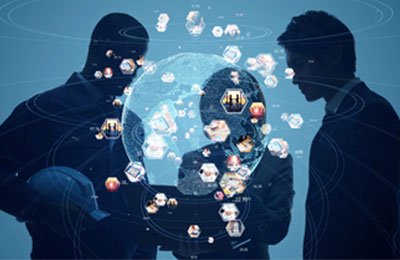
-
工場のボトルネックがどこにあるのかわからない
-
突然の故障の修理には時間がかかる
-
設備投資への抜本的な対策が打てない
-
特定設備の停止が頻発する
データ活用による対策
設備の状態データや作業データを収集し、稼働率の低い設備や設備停止理由の特定を行うことで、「止まらない」工場の実現を目指します。
設備状態の可視化
設備データの自動収集と設備停止理由の登録で、設備状態の可視化が可能です。
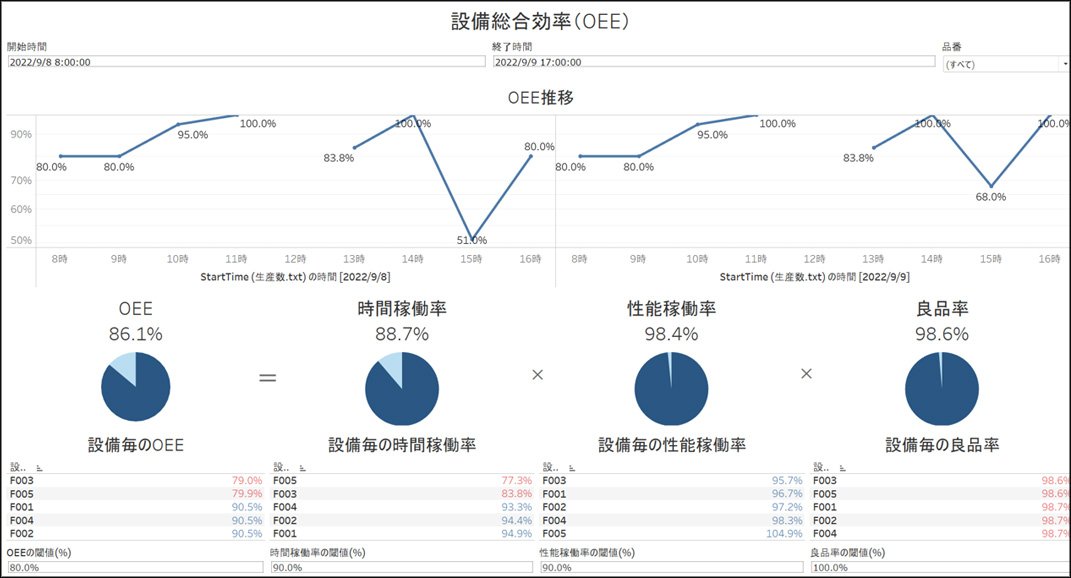
停止理由を特定し、抜本的な対策を実施
設備停止に最も影響を及ぼしている要因を一目で把握し、どの事項を優先して解決すべきかが明確になります。
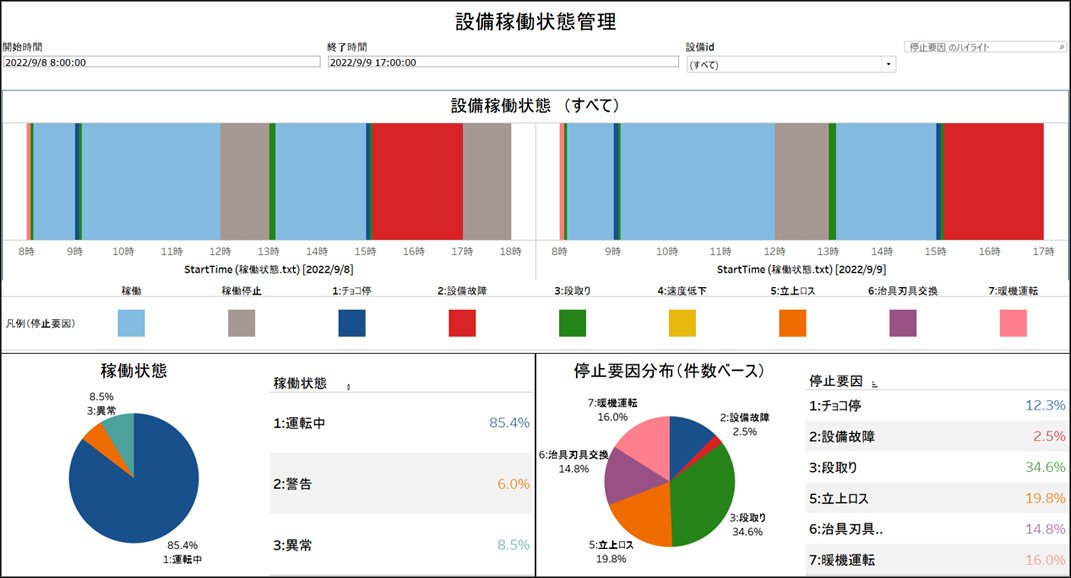
動画で解説
設備総合効率・設備稼働分析ダッシュボード1分37秒
Tableauを活用して工場の設備稼働状態の可視化・分析を行うことで、今後の改善策の検討を行えます。
生産実績・ラインモニターダッシュボード 1分45秒
Tableauを活用して設備の稼働実績状況から問題のある設備を特定します。
2.製造トレーサビリティで製造品質を改善
製造現場における課題
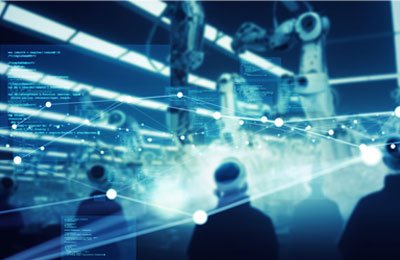
- 不十分な製造工程のデータ収集
- 製造実績データが設備内の蓄積にとどまっている
- 手書き、目検で対応している
- 情報がバラバラに保管されている
- 不良品発生時の原因特定や分析が属人的
- 点在する製造情報を人手によりかき集め、対象と思われる情報を突き合わせている
- これまでの経験と勘で原因の特定を対応している
データ活用による対策
製造工程全体の情報の一元管理と各工程の状態の可視化により、どの工程で、どのような不具合が発生したのか追求し(遡及)、原因分析を行い問題解決を図ることができます。
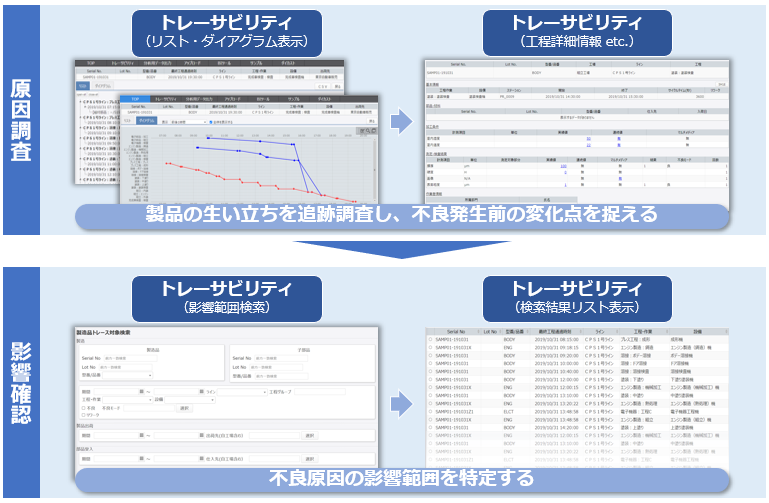
3.製造実績を収集し、実際原価を把握
多品種少量生産が進み、同じライン上で違う製品を生産することが増加し、製品別に実際に掛かった製造時のコストを把握することが難しくなってきています。
製造現場における課題

-
同じラインで違う製品を生産しているため、製品別の製造費が分からない
-
生産にバラつきが発生するため、ロット毎の製造費が分からない
-
原材料や部品の仕入値が時期により違うため、製品原価を把握できない
データ活用による対策
設備や工程から稼働データや製造実績データなどを収集し、一元管理することで、製品別、ロット別に実際に製造するのに掛かった設備や作業者の製造実績を原価管理システムへフィードバックすることが可能になります。また、製造原価や製品価格、作業工程の見直しを図ることが可能です。
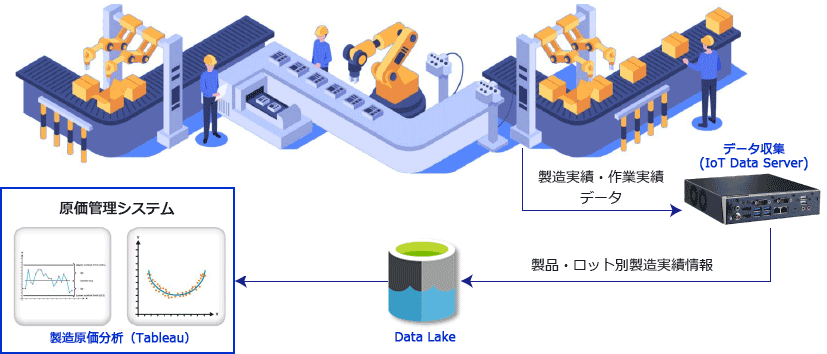
現場ものづくり分析・管理
業務データおよびリアルタイムに収集したIoTデータなどの多様な現場ものづくりのデータを蓄積し、活用することで、現場ものづくりにおけるデータにもとづく業務改善が可能です。
1.設備稼働データを活用した歩留まりの改善
製造現場では、さまざまな原因により不良品が発生することで、歩留りの低下が生じています。
製造現場における課題
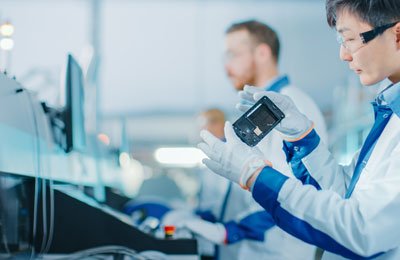
-
材料や部品の不具合
-
作業のばらつき
-
製造環境(温度・湿度)の違いや変化
-
工程間における加工の相関
-
整備の不良、摩耗、劣化
データ活用による対策

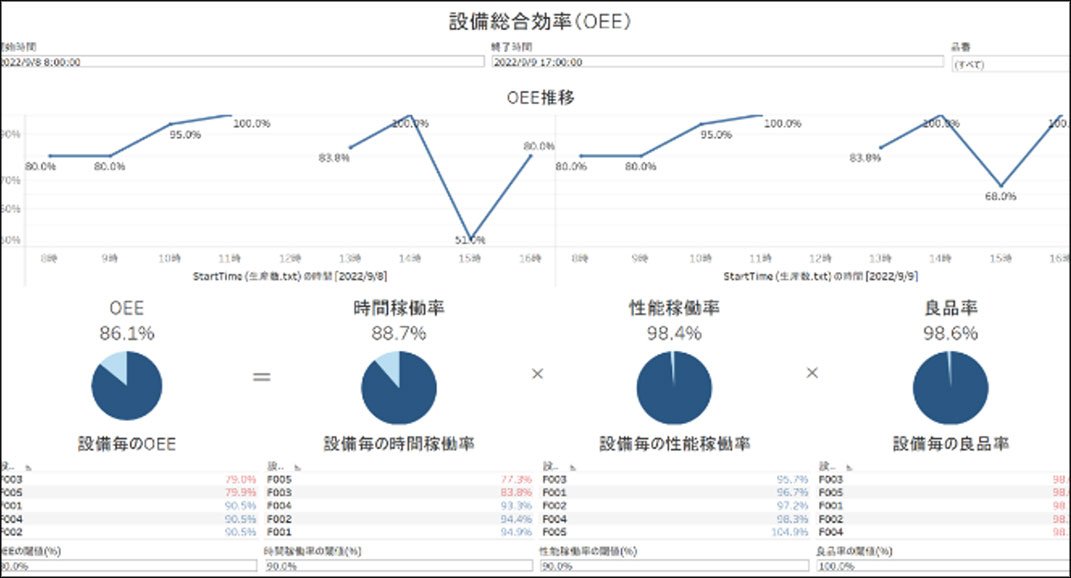
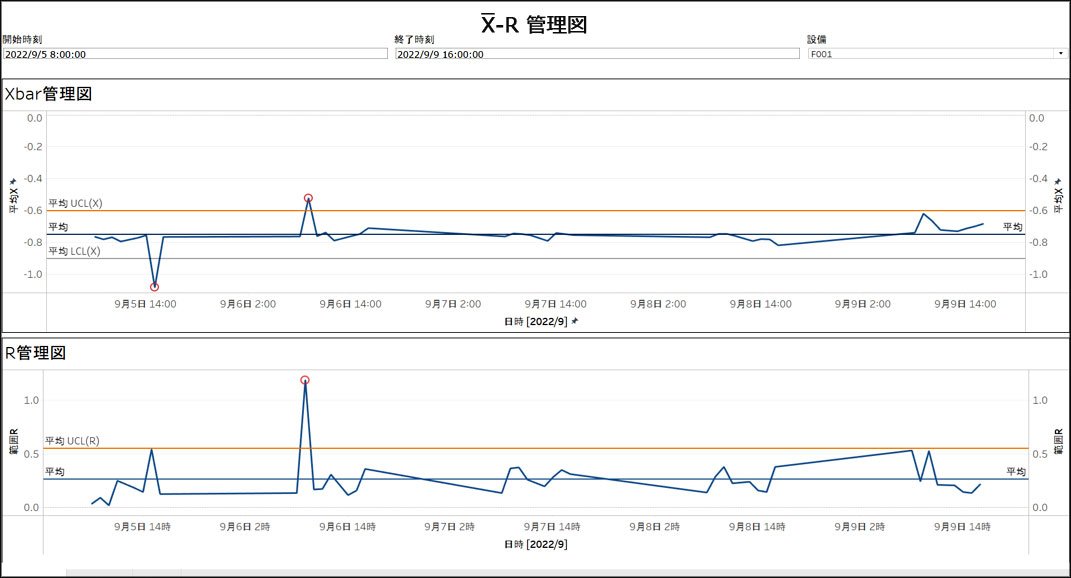
異常判定View Xbar-R管理図 1分19秒
Tableauを活用して製造時の加工状態から異常を捉え、不具合要因などを特定します。
2.設備稼働データとAIの活用による製品品質向上と検査の効率化
目視検査は人間の感覚で行うことから、検査員による判定のばらつきやヒューマンエラーが発生する恐れがあります。また、製品の小型化や要求品質の厳格化が進み、かつ多品種生産が増える中で、検査にかかる負担がいっそう大きくなっています。
加えて、不良品発生の原因特定に熟練作業員のカン・コツで対処する手段も、深刻な人材不足により持続的でなくなりつつあります。
製造現場における課題
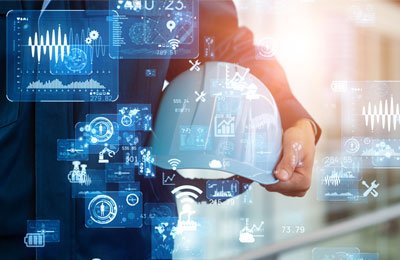
-
全数検査ができない
-
検索結果にばらつきが出る
-
不良品が出荷されてしまう
-
人手が足りない
-
検査を自動化したい
データ活用による対策
AI外観検査
目視検査工程の作業員と検査回数を大幅に削減でき、サンプリング検査から全数検査にすることで、検査品質の改善につながります。
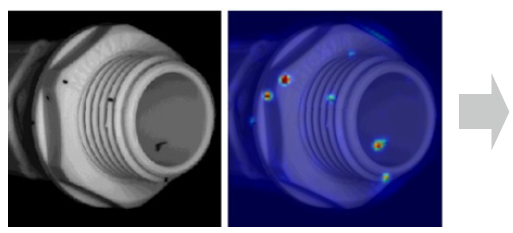
製品不良と設備稼働データの相関分析
AI外観検査の判定結果と設備の稼働データや故障データを掛け合わせ相関分析を行うことで、不良品発生の抑制を目的とした保全活動を行うことが可能です。

3.設備のダウンタイムを削減し、生産効率を改善
生産能力を大きく左右する設備の稼働率。工場では、製造プロセスの停止をまねく、さまざまな問題が発生しています。
製造現場における課題
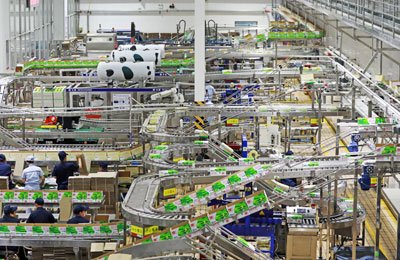
-
予期しない設備の突然の故障
-
設備故障による生産ラインの停止
-
設備障害に伴う生産性・品質の低下
-
ライン停止による納期の遅延
データ活用による対策
AIやダッシュボードテンプレートの活用により、機械や設備の異常を検知し、障害発生前にメンテナンスを実施することで突然の生産停止を防ぐことができます。
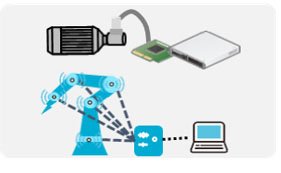
- PLCやセンサーから機械・設備の稼働状態のデータを収集
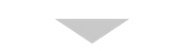
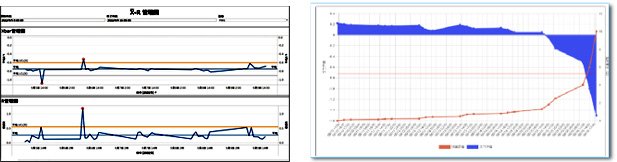
-
回転機械機械学習により故障予兆を検知
-
その他の機械・設備ダッシュボードテンプレートを活用し、Xbar-R管理図などで設備状態を判断
ものづくりDXソリューション詳細資料をご希望の方は、こちらからお申し込みください。
- 製造業 ものづくりDX トップ
- DXソリューション
- DXユースケース
- Profet AI 導入事例
- *その他記載の会社名および商品名は、各社の商標または登録商標です。